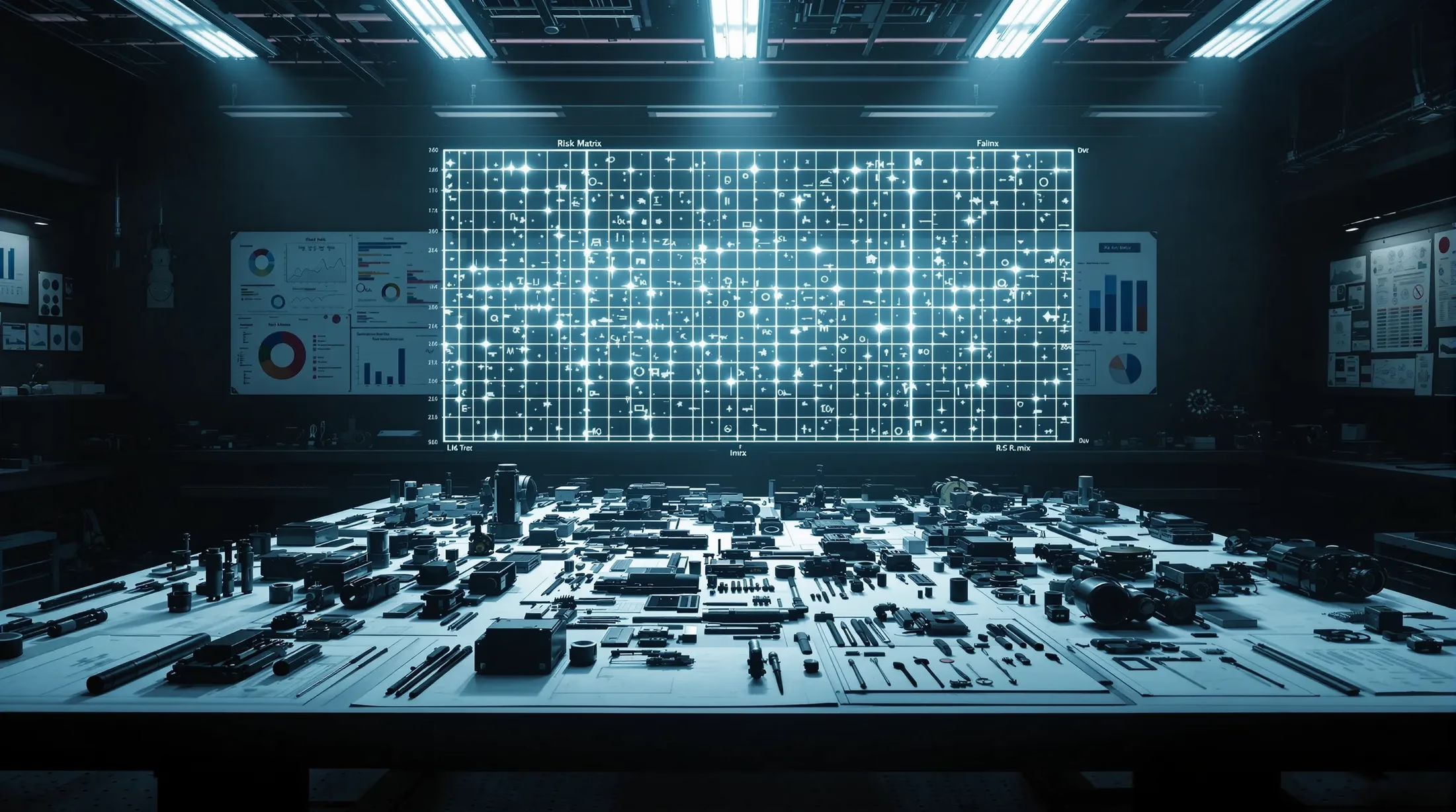
Skuteczne zarządzanie ryzykiem w organizacji wymaga systematycznego podejścia do identyfikacji i analizy potencjalnych zagrożeń. FMEA (Failure Mode and Effects Analysis) stanowi sprawdzone narzędzie, które pozwala przewidzieć i wyeliminować możliwe wady, zanim wpłyną one na jakość produktów lub procesów.
Czym jest FMEA – definicja i cel analizy przyczyn wadliwości i krytyczności
FMEA to systematyczna metoda identyfikacji i oceny potencjalnych wad w produktach, procesach lub systemach. Jej głównym zadaniem jest wykrycie możliwych błędów przed ich faktycznym wystąpieniem, co umożliwia wprowadzenie działań zapobiegawczych minimalizujących ryzyko.
Metodologia koncentruje się na trzech aspektach:
- identyfikacji możliwych sposobów powstawania wad
- określeniu potencjalnych skutków
- oszacowaniu prawdopodobieństwa wystąpienia
Historia i rozwój metody FMEA w zarządzaniu jakością
Początki FMEA sięgają lat 40. XX wieku, gdy amerykańskie siły zbrojne stworzyły procedurę MIL-P-1629 do oceny wpływu awarii na misje wojskowe. NASA wykorzystała tę metodologię w programie Apollo w latach 60.
Przełomowy moment nastąpił w latach 70., gdy Ford Motor Company wdrożył FMEA po problemach z modelem Pinto. W 1980 roku amerykańscy producenci samochodów wspólnie opracowali standardy FMEA, które później stały się częścią systemu zarządzania jakością w motoryzacji.
Rodzaje FMEA: FMEA procesów, FMEA produktów, FMEA systemów
Rodzaj FMEA | Zastosowanie | Obszar analizy |
---|---|---|
Design FMEA (D-FMEA) | Analiza konstrukcji i projektowania wyrobu | Komponenty, podsystemy i ich interakcje |
Process FMEA (P-FMEA) | Analiza procesu wytwarzania lub świadczenia usługi | Etapy procesu produkcyjnego |
System FMEA (S-FMEA) | Analiza całego systemu | Interakcje między produktami i procesami |
Jak przeprowadzić analizę FMEA: etapy i metodyka
Analiza FMEA wymaga systematycznego podejścia i zaangażowania interdyscyplinarnego zespołu. Proces składa się z następujących etapów:
- Zdefiniowanie systemu, produktu lub procesu do analizy
- Powołanie zespołu specjalistów
- Identyfikacja potencjalnych trybów awarii
- Analiza skutków awarii
- Identyfikacja przyczyn wad
- Ocena ryzyka (wskaźnik RPN)
- Opracowanie działań korygujących
- Wdrożenie zmian i ponowna ocena
Ocena ryzyka: skala prawdopodobieństwa, skala skutków, skala wykrywalności
Ocena ryzyka w FMEA opiera się na trzech 10-punktowych skalach:
- Prawdopodobieństwo (Occurrence) – od 1 (rzadziej niż 1/1 500 000) do 10 (częściej niż 1/2)
- Skutki (Severity) – od 1 (nieznaczny wpływ) do 10 (zagrożenie życia)
- Wykrywalność (Detection) – od 1 (pewne wykrycie) do 10 (niewykrywalne)
Wskaźnik priorytetu ryzyka (RPN) stanowi iloczyn tych trzech parametrów i może wynosić od 1 do 1000. Wartości powyżej 100-125 zazwyczaj wymagają natychmiastowej interwencji.
Zastosowanie FMEA w różnych branżach
Metodologia FMEA znajduje szerokie zastosowanie w sektorach przemysłu, gdzie bezpieczeństwo i niezawodność stanowią podstawowe priorytety. Przemysł motoryzacyjny, jako pionier wdrażania FMEA, uczynił z tej analizy standardowy wymóg dla dostawców i producentów części. Firmy takie jak Ford, General Motors czy Toyota regularnie wykorzystują FMEA podczas projektowania nowych modeli pojazdów i procesów produkcyjnych, minimalizując ryzyko kosztownych wad.
- Przemysł lotniczy i kosmiczny – FMEA zapewnia bezpieczeństwo systemów, gdzie drobna usterka może prowadzić do poważnych konsekwencji
- Sektor medyczny – projektowanie urządzeń, leków i procedur klinicznych zgodnie z wymogami unijnymi
- Przemysł elektroniczny – identyfikacja wad w złożonych układach elektronicznych
- Sektor chemiczny – zapobieganie awariom mogącym prowadzić do skażenia środowiska
- Energetyka i przemysł jądrowy – przewidywanie i eliminacja zagrożeń dla zdrowia publicznego
Przykłady zastosowania FMEA w praktyce
Organizacja | Zastosowanie | Rezultat |
---|---|---|
NASA | Analiza komponentów statku kosmicznego w programie Apollo | Zwiększenie bezpieczeństwa misji kosmicznych |
Toyota | Analiza układu napędowego w modelu Prius | Wczesne wykrycie problemów w systemie hybrydowym |
Klinika Mayo | Analiza procesu podawania leków | 60% redukcja błędów medycznych |
Korzyści płynące z wdrożenia FMEA w organizacji
- Zwiększenie niezawodności produktów i procesów poprzez wczesne wykrywanie potencjalnych wad
- Znacząca redukcja kosztów operacyjnych – nawet 100-krotnie niższe koszty naprawy błędów wykrytych w fazie projektowania
- Skuteczniejsze zarządzanie ryzykiem dzięki obiektywnej ocenie zagrożeń
- Wzrost satysfakcji klientów poprzez dostarczanie bardziej niezawodnych produktów
- Rozwój kultury ciągłego doskonalenia w organizacji
Najczęstsze błędy przy przeprowadzaniu analizy FMEA
- Powierzchowna identyfikacja potencjalnych wad – koncentracja wyłącznie na oczywistych problemach
- Nieodpowiedni dobór członków zespołu – brak interdyscyplinarnego podejścia
- Zbyt późne przeprowadzenie analizy w cyklu rozwoju produktu
- Subiektywna ocena parametrów ryzyka zamiast oparcia się na danych historycznych
- Traktowanie FMEA jako jednorazowego działania zamiast procesu ciągłego
Narzędzia i oprogramowanie wspierające proces FMEA
Podstawą skutecznej analizy FMEA jest odpowiednie wsparcie narzędziowe, które usprawnia pracę zespołu i gwarantuje spójność metodologiczną. Diagram procesu stanowi fundamentalne narzędzie wizualizujące kolejne etapy produkcyjne lub projektowe, umożliwiając precyzyjną identyfikację punktów krytycznych. Uzupełnieniem diagramu jest burza mózgów, angażująca zespół w kreatywną identyfikację potencjalnych zagrożeń.
- APIS IQ-RM – zaawansowane funkcje obliczania wskaźnika RPN
- Relyence FMEA – tworzenie bibliotek typowych wad
- Plato SCIO – generowanie raportów i śledzenie działań
- FMEA-Pro – dostęp do analiz z dowolnego miejsca
- Xfmea – praca zespołowa w czasie rzeczywistym
Rozwiązania oparte na chmurze zyskują coraz większą popularność, eliminując konieczność lokalnej instalacji oprogramowania. Systemy te zapewniają elastyczny dostęp do analiz FMEA z różnych urządzeń. Warto zaznaczyć, że nawet arkusze Excel mogą skutecznie wspierać analizy FMEA w mniejszych organizacjach, pod warunkiem właściwej metodyki pracy.
Integracja FMEA z innymi metodami zarządzania jakością
Analiza FMEA osiąga najwyższą efektywność w połączeniu z innymi metodami zarządzania jakością. Szczególnie wartościowa jest integracja z metodologią Six Sigma, gdzie FMEA dostarcza danych wejściowych do cyklu DMAIC.
- QFD (Quality Function Deployment) – przekładanie wymagań klienta na parametry techniczne
- APQP (Advanced Product Quality Planning) – planowanie jakości produktu
- SPC (Statistical Process Control) – statystyczne sterowanie procesem
- Diagram Ishikawy – pogłębiona analiza przyczyn problemów
- Lean Manufacturing – eliminacja marnotrawstwa poprzez wczesną identyfikację defektów
Przyszłość FMEA: trendy i nowe podejścia w analizie ryzyka
Rozwój FMEA zmierza w kierunku automatyzacji i integracji z nowoczesnymi technologiami. Cyfrowe bliźniaki (digital twins) umożliwiają testowanie scenariuszy awarii w środowisku wirtualnym, a sztuczna inteligencja wspomaga identyfikację potencjalnych problemów na podstawie danych historycznych.
Trend | Charakterystyka |
---|---|
Harmonizacja standardów AIAG-VDA | Ujednolicone podejście do analizy łańcuchów przyczynowo-skutkowych |
Ryzyko funkcjonalne | Analiza wpływu wad na funkcjonalność z perspektywy użytkownika |
Podejście adaptacyjne | Dostosowanie metodologii do specyfiki branży i procesu |