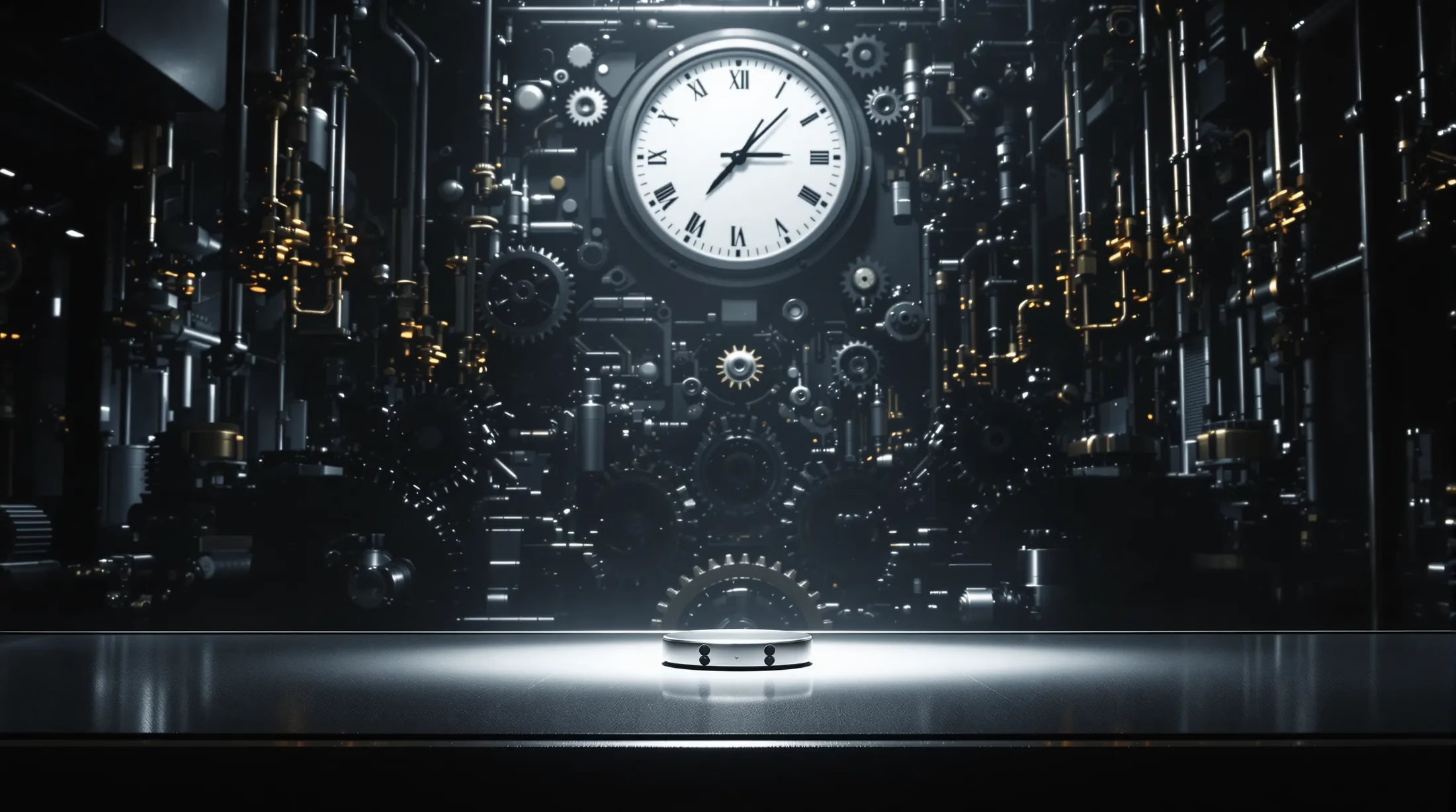
Nowoczesne przedsiębiorstwa nieustannie poszukują metod optymalizacji procesów produkcyjnych. System Just-in-Time (JIT) stanowi sprawdzone rozwiązanie, które rewolucjonizuje sposób zarządzania produkcją i zapasami. Poznaj zasady działania tej metody oraz jej wpływ na efektywność przedsiębiorstwa.
Czym jest produkcja Just-in-Time (JIT)?
Produkcja Just-in-Time to strategia zarządzania produkcją oparta na dostarczaniu materiałów i komponentów dokładnie w momencie ich wykorzystania w procesie wytwórczym. System ten eliminuje nadmierne magazynowanie oraz redukuje koszty związane z przechowywaniem materiałów.
Metoda JIT skupia się na eliminacji marnotrawstwa w procesie produkcyjnym, co przekłada się na zwiększenie efektywności operacyjnej. Przedsiębiorstwa produkują wyłącznie to, co jest aktualnie potrzebne, bazując na rzeczywistym zapotrzebowaniu. Takie podejście pozwala uwolnić kapitał zamrożony w zapasach i lepiej wykorzystać przestrzeń magazynową.
Historia i rozwój metody JIT
Metoda Just-in-Time narodziła się w Japonii lat 50. XX wieku jako element Toyota Production System (TPS). Jej twórcą był Kiichirō Toyoda, założyciel Toyota Motor Corporation, a rozwinął ją Taiichi Ōno, inspirując się działaniem amerykańskich supermarketów.
W latach 70. i 80. XX wieku, wraz z rosnącą pozycją japońskich firm na światowych rynkach, JIT zyskało międzynarodowe uznanie. Szczególnie przemysł motoryzacyjny docenił zalety tego systemu, który następnie rozprzestrzenił się na inne sektory gospodarki.
Podstawowe zasady JIT
- Produkcja na żądanie – uruchamianie procesów wytwórczych w odpowiedzi na faktyczne zamówienia
- Minimalizacja marnotrawstwa (muda) – eliminacja siedmiu rodzajów strat:
- nadprodukcji
- czekania
- transportu
- nadmiernego przetwarzania
- zapasów
- zbędnego ruchu
- defektów
- Ciągłe doskonalenie (kaizen) – systematyczne usprawnianie procesów produkcyjnych
- Synchronizacja procesów – zapewnienie płynnego przepływu materiałów i informacji
- Współpraca z dostawcami – budowanie trwałych relacji opartych na zaufaniu
Korzyści z wdrożenia JIT
Implementacja systemu Just-in-Time przynosi przedsiębiorstwom wymierne korzyści finansowe i operacyjne. Firmy zyskują większą elastyczność w reagowaniu na potrzeby rynku, a synchronizacja procesów produkcyjnych prowadzi do efektywniejszego wykorzystania zasobów.
Redukcja kosztów i zapasów
System JIT pozwala na znaczące zmniejszenie poziomu zapasów magazynowych, często o 50-90%. Przekłada się to na:
- niższe koszty powierzchni magazynowej
- mniejsze wydatki na ubezpieczenia i podatki
- redukcję kosztów obsługi magazynów
- zmniejszenie ryzyka przeterminowania materiałów
- szybsze wprowadzanie innowacji produktowych
Poprawa jakości i efektywności
Wdrożenie JIT przekłada się na wyższą jakość produktów poprzez:
- szybsze wykrywanie i korygowanie defektów
- redukcję ilości przeróbek i odpadów
- lepszy przepływ materiałów i informacji
- standaryzację procesów produkcyjnych
- minimalizację czasów przezbrojeń i przestojów
Wyzwania i ryzyka związane z JIT
Wdrożenie systemu Just-in-Time wymaga pokonania szeregu wyzwań. Najważniejsze z nich to konieczność nawiązania ścisłej współpracy z dostawcami oraz ciągłe monitorowanie i optymalizacja procesów produkcyjnych. System wymaga precyzyjnego planowania, sprawnej komunikacji wewnętrznej oraz gotowości na zmiany w kulturze organizacyjnej.
Rola dostawców w systemie JIT
Dostawcy stanowią integralną część procesu produkcyjnego w systemie Just-in-Time. Synchronizacja dostaw wymaga nie tylko punktualności, ale także utrzymania niezmiennej jakości dostarczanych komponentów. W praktyce oznacza to budowanie długoterminowych, partnerskich relacji z wyselekcjonowaną grupą sprawdzonych dostawców, zamiast ciągłego poszukiwania najtańszych opcji na rynku.
- Optymalna lokalizacja – bliskość dostawców względem zakładu produkcyjnego minimalizuje ryzyko opóźnień
- Częstotliwość dostaw – gotowość do realizacji mniejszych, ale częstszych partii materiałów
- Stabilność współpracy – długoterminowe relacje oparte na wzajemnym zaufaniu
- Jakość komponentów – utrzymanie stałych standardów jakościowych
- Elastyczność działania – zdolność do szybkiego reagowania na zmiany w zapotrzebowaniu
Zarządzanie ryzykiem i wahania popytu
Brak zapasów magazynowych w systemie JIT sprawia, że przedsiębiorstwa muszą szczególnie uważnie podchodzić do zarządzania ryzykiem. Firmy stają się wrażliwe na wszelkie zakłócenia w łańcuchu dostaw – od strajków po katastrofy naturalne czy globalne kryzysy.
- Strategie minimalizacji ryzyka:
- dywersyfikacja źródeł dostaw
- opracowanie planów awaryjnych
- zaawansowane systemy prognozowania popytu
- elastyczne systemy produkcyjne
- monitoring łańcucha dostaw
JIT jako element lean management
Just-in-Time stanowi fundamentalny filar filozofii lean management, rozwiniętej przez Toyotę. System JIT, koncentrując się na optymalizacji dostaw materiałów, współgra z szerszym zestawem zasad lean, ukierunkowanych na eliminację marnotrawstwa (muda) w procesie produkcyjnym.
Połączenie JIT z pozostałymi elementami lean umożliwia systemowe podejście do redukcji zbędnych działań, nadprodukcji i magazynowania. Efektem jest wyższa wydajność operacyjna, krótsze cykle produkcyjne oraz zwiększona elastyczność w reagowaniu na zmiany rynkowe.
Integracja JIT z innymi metodami lean
- System kanban – wizualne zarządzanie przepływem materiałów i informacji
- Metoda 5S – organizacja przestrzeni produkcyjnej:
- sortowanie
- systematyka
- sprzątanie
- standaryzacja
- samodyscyplina
- SMED – szybkie przezbrojenia maszyn
- Poka-yoke – zapobieganie błędom
- Jidoka – automatyzacja z ludzkim nadzorem
Przykłady wdrożeń JIT w różnych branżach
Firma | Branża | Osiągnięcia |
---|---|---|
Toyota | Motoryzacja | Redukcja kosztów produkcji o 30%, zwiększona elastyczność |
Dell | Elektronika | Konfiguracja na żądanie, dostawy kilka razy dziennie |
McDonald’s | Gastronomia | Przygotowanie posiłków na bieżąco, minimalizacja strat |
Zara | Odzież | Wprowadzanie kolekcji w 2-3 tygodnie |